これまでの経緯
既に、オイルクーラーの取り付け金具を製作し、さあ取り付けようと思っていた。夏を前にして5月のことだ。
しかし、なんかしっくりこない。なんか金具が強度不足のような気もするし、コアが大きくてWの容姿からみてバランスが取れていないかも、という思いも抱くようになった。 そこで、思案した結果、取り付けようと思っていたZZR1100のオイルクーラーを諦め、改めて少々小ぶりで、かつオイル上出し状態での取付けが可能そうなものを物色した。もちろん、カワサキ車で。 そして手に入れたものがGPZ1000RXのもの。6月のことだ。ヤフオクで1000円!
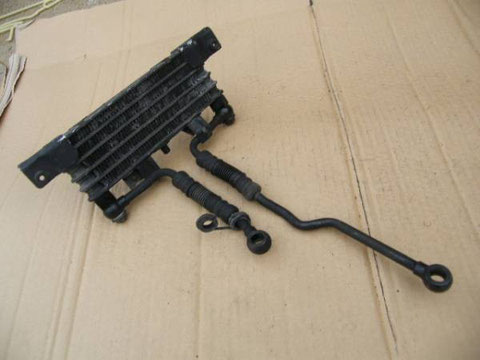
そして、箱根ミーティングで様々なWのオイルクーラーをチェック。このコアを使っているものは皆無だったので、じゃあオリジナル性もあるし、これで決まりだな、と決意した(笑)。
それから早く実行せねばと思いつつ、いつものように数か月経ち、夏場の油温実態が判明したので、さあタイミングはバッチリ、オイルクーラーをつけると、どれくらい効果があるか実験できるぞということで改めて取り付け作業をスパートすることにした。
取付け金具製作
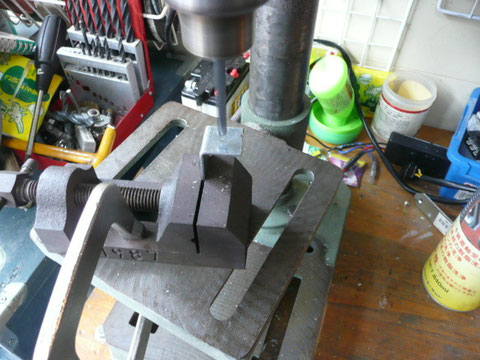
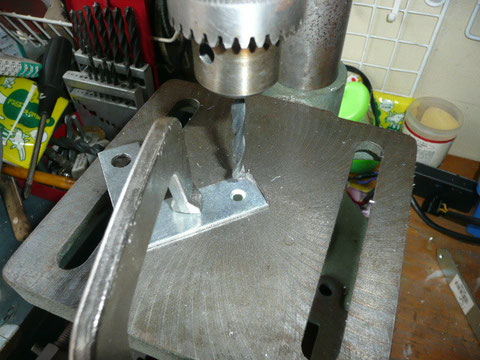
2012/09/15
市販の大工用具?の金具を適切な寸法に切り出し、本来釘が入るべき穴をボール盤で拡大してネジが入るようにする。
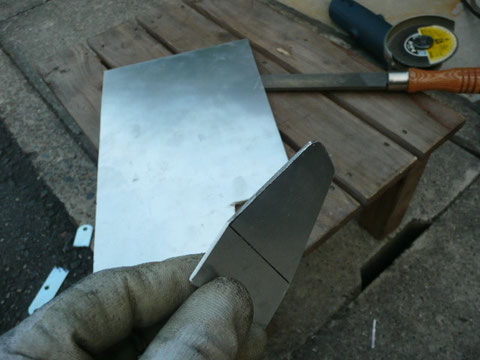
2mm厚のアルミ板を切り出す。
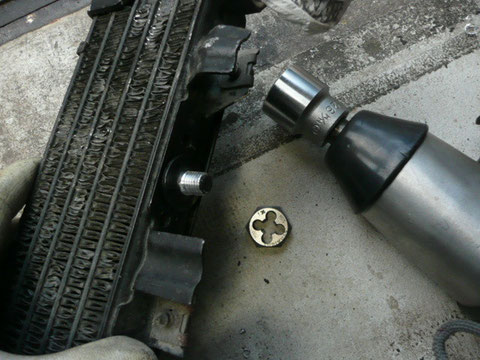
オリジナルでは単なる突起物だったところにM10×p1.25のネジを切る。面倒なので、インパクトでネジ切り。手動でやるより手っ取り早い。あまりおススメできない方法だけども、このスピード感と手軽さはやめられません。
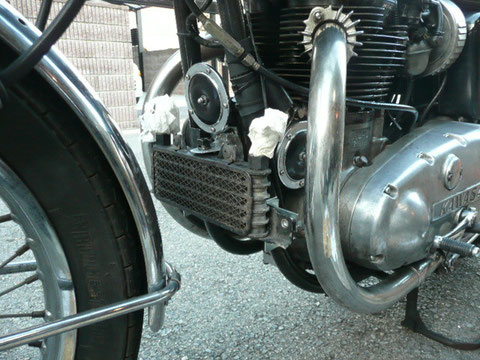
こんな感じで仮付完了。
あまり低い位置にすると、砂とか跳ね上げたものがコアを破損しそうなので少し高めの位置とした。
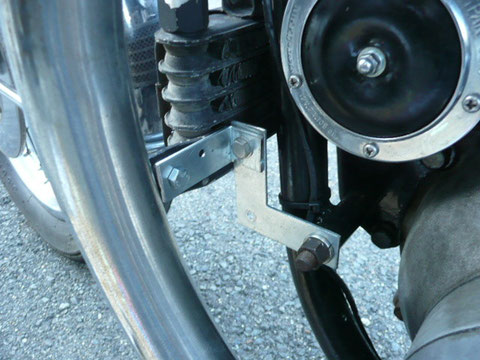
仮止めなので、切り出したままで未塗装だが、寸法的にはこれで良さそう。ちなみに、金具はスチール製2mm厚なので強度的には大丈夫だろう。不足があれば、L型部分を二枚重ねにしても良いかも。
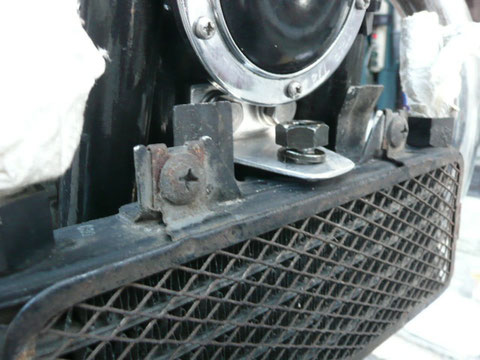
これも仮止め。
L金具の後ろ側にゴム板を挟んでいて一応、柔支持構造にはしている。ゆるみ防止のため、ボルトにはワイヤーロックしておこうかなあと思っている。
コアのお掃除
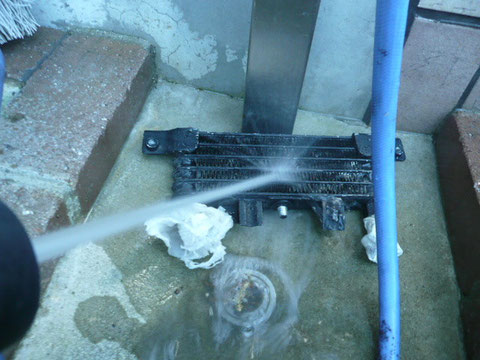
コアが一部小砂やホコリで目詰まりしているので、水道水で掃除。
圧水を吹き付けると、出てくるわ泥水が・・・。
内部に水が入らないよう注意しながら、思いっきりフィンの隙間を掃除した。
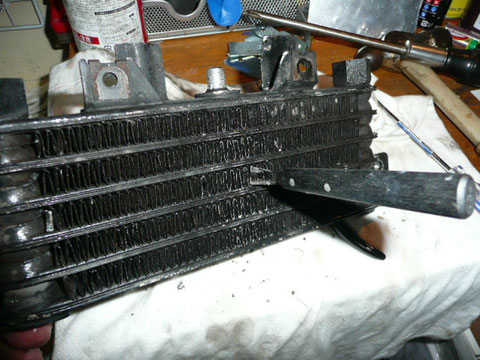
それから、精密ドライバーのマイナスや、小さめのコテなどを駆使して、隙間のゴミ(特に小砂)を丹念に取り除くとともに、コアの変形を矯正していく。写真のコテを使うと、コアを貫通してゴミ掃除できる。そしてコテを引き抜く際に、ちょっとしたコツをつかめばフィンが綺麗に起きてくる。
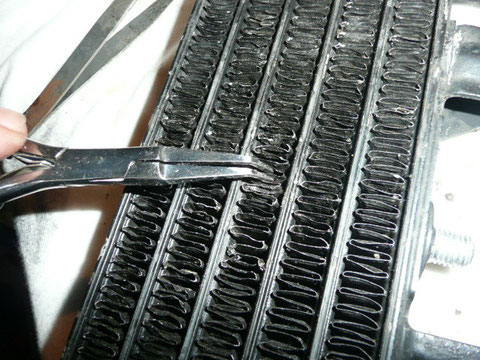
先端が平滑なラジオペンチも非常に便利。
フィンの隙間にもフィットする。これをニギニギやって一枚毎に丁寧にフィンを整形していく。
上側・・・ビフォー
下側・・・アフター
アフターで少し白くなっているのは、コテやドライバーで矯正した際に塗装が剥げたため。コアを光に透かしてみると、ビフォーでは約3割くらい閉塞していたが、アフターではほぼ100%光が通過した。その分、冷却効率も増しているはずだ。
余談だが、電車のエアコンの放熱器は屋根上に積まれているが、これが数年も経つと凄い汚れで目詰まりがひどくなり故障の大きな原因となる。だから定期的に高圧水でフィンの隙間を丁寧に掃除している。フィンものには掃除が大切なのはどの乗り物も同じ。
今後は、コア、保護カバー、取付けステーの塗装と、オイルホースのフィッティングだ。さて、ミッションをずらすのは面倒だから、ちょっと姑息な手段を選ぼうかと思っている。でも、見栄えとホース接続方法としての美学は忘れずに・・・。
サンドブラスト
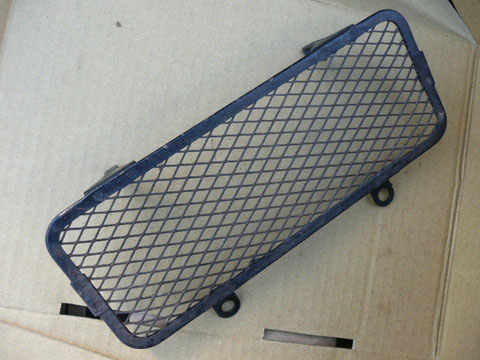
2012/9/17
昨日の続き・・・
だいぶん錆びているコア保護版。
久しぶりにサンドブラストでもやってみるか。
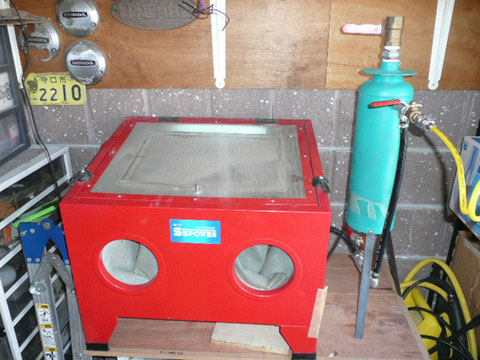
うちのサンドブラストキャビネットは、通販で1万数千円の安物。
隣にあるのは消火器を改造して製作した直圧ブラストユニット。2kgf/cm2程度の低圧エアで、十分なサンブラが可能だ。消火器の上から砂を入れて、溜まった砂の上面にエアが加圧し、さらに落下した砂を同圧のエアで吹き飛ばすという原理。結構威力ある。
ちなみに、左に写っているナンバーは昭和62年頃に乗っていたDJ1-Lのナンバープレート。ナンバーだけ盗難されて発見されたものだったような気がする。ナンバー再発行してもらったため、このナンバーが浮いた格好に。
もうひとつ、その上の何やら丸い品物が三つ。これを見て、何の部品かわかる人は?破損しているやつは、筑波サーキットでの走行時に大転倒したときのもの。平成2年のテイストオブフリーランスのドーバー1クラスに出場するための練習走行時!本番時には、ショップワークスのZ1000Rにラップされましたが(笑)。むちゃくちゃ速いんですもの。ライダーも国際A級! ほぼノーマルの私には太刀打ちできませんでしたわ~。
話が逸れました。
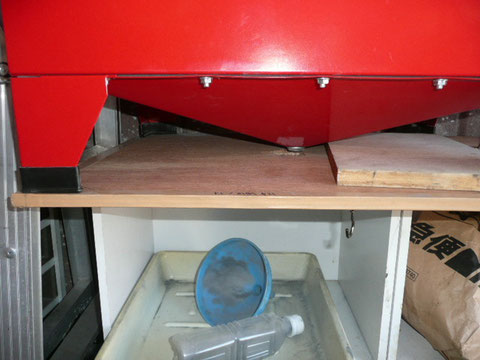
このサンブラキャビネットは、書棚の上にべニアを置いて載せてある。砂を取り出すときには、べニアと書棚に開けてある穴のボルトを外す。すると、ジャーっ、と下のトレイに吐き出されるという按配。かなり砂まみれになるので、マスクは必需品だ。
さて、サンドブラストを終えて次の作業に掛かろうとしたときに、とらのすけさんから携帯に電話が。「オイルクーラーの作業中ですか?」と、図星。まるで私の行動を見ているようだ。それで、近いうちに一杯飲みに行くことになりました。プレゼントがあるようなので、楽しみです。ありがたいですね、Wの仲間というのは。
塗装と焼き付け
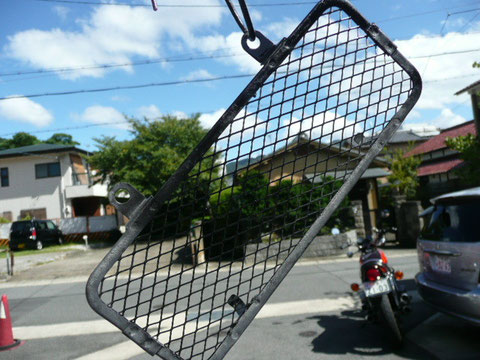
サンブラしてすっきりした後、錆落とし剤を塗布してリン酸皮膜を生成させてから塗装へ。天気が良いが少し風が強くて塗料が飛散しまくり・・・。
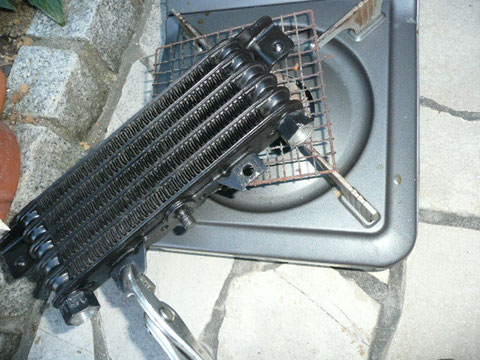
オイルクーラー本体は真鍮ブラシで軽く掃除した後、脱脂して耐熱スプレーで塗装。その後は、いつものように直火焼き(笑)。窯があればいいんだが、そんなものないので、カセットコンロで炙る。原始的だが、これを全体にまんべんなくやってやると、それなりに艶やかでしっとりした強固な塗膜ができること請け合い。炙った後、自然冷却してから触ると、ラッカースプレーとは違った感触だ。
オイルホース
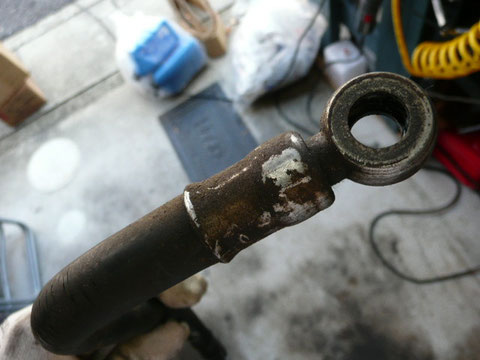
オイルホース。安価で購入したごちゃ混ぜパーツ群の中に入っていたもの。これがいわゆる分解可能なWのオイルホース。
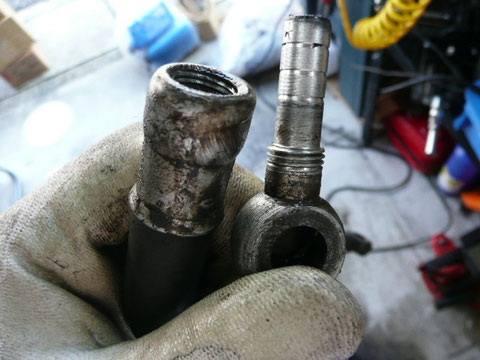
バンジョー部分がねじ込みになっている。ホースにムニュッと差し込んだ後、数回回転させて固定するという仕組みだ。何でこんな構造にしたんだろう。ホースだけ交換することを想定したのかな?あるいは一体モノの製法が無かったのかな?
さて、私のW3にはどうつけるか。
ミッションをずらすのは面倒なので、やはり在姿のままで作業を行うことにする。
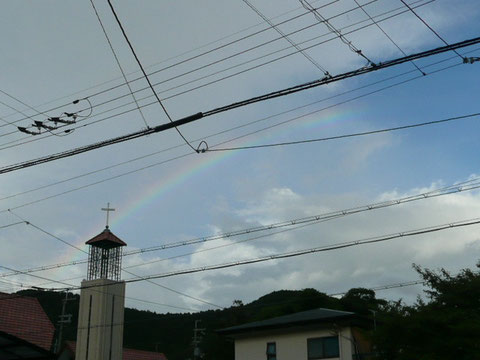
夕方、少し小雨が降ったと思ったら、東の空に大きな虹が。
通りがかった高校生くらいの女の子が、「うあ、やべ~」とか言いながら空を見るので、何だろうと思って見上げると、これ!
本日の作業はこれまで。
三連休でできたこと
・オイルクーラー本体の整備
コア掃除、コア整形、不要ステー切除、角部グラインダー処置、耐熱塗装
・コア保護カバーの整備
錆落とし(サンドブラスト)、塗装
・ステーの作成
ホームセンターで売っている金具@100円程度のもの×4個を、切断、穴あけ、角部グラインダー処置、塗装
ガレージの掃除やら、部品の整理やら何やらいろんなことをごちゃまぜにやっていたので、思った程は進捗しなかったが、あと一日あれば車体に取り付けられそうだ。
ホース継手の製作
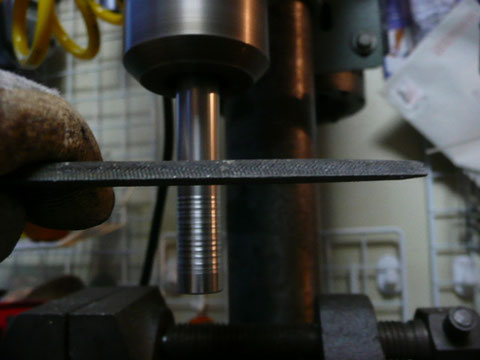
2012/9/22
W3のオイルホースはΦ9mm用の既製品のホース継手ではスカスカ。あいにくΦ10mm用のものは近くのホームセンターにはない。そこでどうしようか、いくつか案を考えてみたが、結局もっとも安直な案に落ち着いた。それは、外径Φ9.5mmのステンレスパイプを使うもの。分解可能なバンジョー部を取り外し、その代わりにこいつを深く差し込んで、ゴム部でパイプバンドで縛り上げるというもの。クランクケースからのリターン側ホースをぶち切ってしまわないので、いつでもオリジナル状態に戻すことができるようになる。
パイプをホースに差し込んだ際に、少しでも圧接部分の摩擦係数が上がるように、パイプに傷をつけておく。パイプをボール盤にくわえて回転させ、ヤスリで微小な溝を多数つける。もちろん、抜け側にエッジが出るように、ヤスリは半丸でカーブ側を写真の方向に向ける。
パイプはアルミか真鍮でも良かったのだが、それも近所のホームセンターには適当な寸法のモノが無かったのでステンレスにしたというもの。
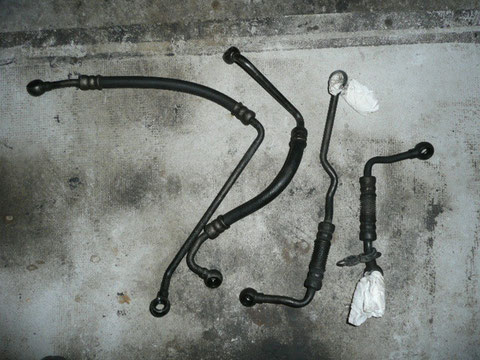
オイルクーラーにつなぐ部分はどうしようか。
写真は、手元にあるホース群。ZZR1100用とGPZ1000RX用のもの。これらの中から、丁度いい按配になりそうなものを、適当にぶち切って流用することにする。さて、どんな感じになるだろうか楽しみ。
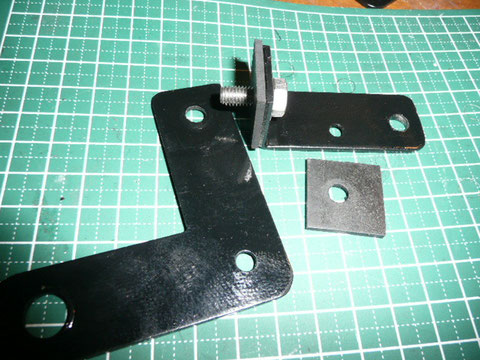
塗装した金具。接続部分にはゴム板を挟んでおき、柔支持にしておく。ということは、逆にWの振動でボルトが緩んでしまうかもしれない。そこで、この部分のボルトはワイヤーロックしましょう。
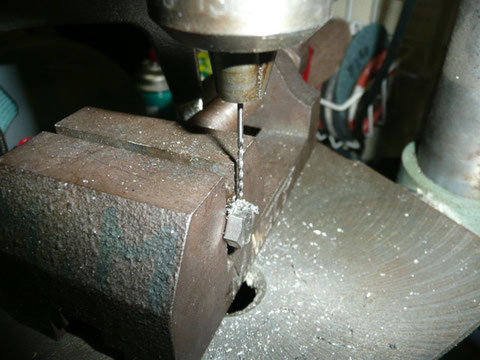
-
#1
やってますね!、バンジョーばらすという方法があったか!気づかなかった
そうすれば油圧配管買ってくれば繋げますね、目からウロコです
私もオイルクーラー付けかけましたがエンジン下部を配管するためにバンジョーの向きを変えるのに
結局外さないといけないと思い挫折しました、リターンは上側なんですよね
仕上がりを楽しみにしています
-
#2
補足です、素人的な考えですが、ボール盤は出来るだけゆっくり回して
キリが食い込んでいくのを助けるだけというか、油さしながら
説明するのはむつかしいです、かなり優しくやらないと細いキリはすぐ折れます、
キリを研げば、引っかかるし奥が深いです、ここらでプロの意見が聞きたいですね
-
#3
プロじゃないけど呼ばれましたでしょうか。
実は、仕事で、ドリル穴開けを毎日やっていますが、
2ミリ位のハイス鋼のドリルは結構折れやすいですので、
私も仕事で折りまくってましたよ。
細いドリルは 卓上ボール盤の最高回転数を使います。
ドリルが太くなるほど 回転数を下げると良いです。
計算式を今、覚えてないので書けません。スミマセン
深穴あけは、一回の切り込み量をドリル径の半分位にして
こまめにステップ送りして、切り屑を排出してやれば、
ドリルは折れにくいです。
ドリルの研ぎ方でも切り屑の出方が変わります。
材料が軟鋼なら大した事ないですが、
ステンレスの様な粘い材質には切削油(極圧剤入り)
スプレーを使っています。
熱でドリルが焼けるとへたりやすいですので、冷やす為にも、切削油は必要みたいです。
職場では、水溶性切削油を使用していますので、
刃物、工具の冷却性が良くて長持ちします。
エンジンオイルを筆で塗ってやってもいけると思います。
(極圧剤はエンジンオイル添加剤にも使われていますよ)
参考になりましたら活用してください。 -
#4
姫路の松居さん
実は、Φ12mmの丸棒中心にΦ9mmの長穴を設け、外側中央部にΦ12×p1.25のネジ部をl=5mm程度で作り、丸棒のネジ部以外は外径Φ10mmに削り落とそうとしてました。すると、リターン側のネジ部にはきちんとねじ込めますしね。でも、大変面倒くさそうなのでやめました。Φ12×p1.25×L40の細目ボルトの頭にΦ12×P1.25のネジ部を作ってそこに同じボルトをねじ込み、一体化したボルトの中心に長穴を設けて外径をΦ10mmに削り落とすな~んてアイデアも。いずれにせよ、無駄に労力使いそうなんで没。でも、試したくなる工作ではあります。
仕上がりまで、もう少し?! ご期待に応えられるかな?
-
#5
とらのすけさん
ありがとうございます。さすがプロ!!
>細いドリルは 卓上ボール盤の最高回転数を使います。ドリルが太くなるほど 回転数を下げると良いです。
そうなんですね。昔、工場実習でやった様な気もしますが、今となっては無頓着すぎました。
>一回の切り込み量をドリル径の半分位にしてこまめにステップ送りして、切り屑を排出してやれば、ドリルは折れにくいです
な~るほど!これは即実践したいと思います。非常に具体的でわかりやすいです。
>切削油は必要みたいです
そうですよね。私はホームセンターの安物ですけど使ってます。
WEBで調べてみると、材質毎の適切なドリル外周の切削速度が分かりました。この数値をミリ換算して、ドリル外周で割れば、rpm/min(毎分の回転数)が求まりますね。
・標準的な鉄 20m/min。
・アルミ材料 40m/min。
・ステンレス材 10~12m/min。キーキーと音がするようなら、一旦7m/minに落とす。
今回の私のボール盤のセッティングからすると、回転数が早すぎたかな?キーキー言ってましたからね、折れる前には。ステンレスボルトでしたので、加工硬化してしまったのでしょう。ドリルを送ろうにも送れないくらい材質が固くなってしまってましたからね。でも、1本目の加工の時には、全く問題なかったんですけどね~。
明日、できれば再チャレンジしてみよう。
コメントをお書きください
姫路の松居 (月曜日, 17 9月 2012 19:32)
やってますね~取り付け後の油温の変化が気になります
私もやっとポンコツボール盤とスライドバイス手に入れました
とらのすけ (月曜日, 17 9月 2012 20:05)
松居さんも遂に工作機械を入手されたのですね。
まつさん、CB-Fでドーバー出てたなんて、凄すぎます。
オイルクーラー完成たのしみです。
ダブル松さんに?かなり遅れをとってますが、マイペースで私、いきますです。(爆沈)
まつ (月曜日, 17 9月 2012 22:41)
姫路の松居様
油温の変化、楽しみですね。大体―10℃位の効果でしょう。工作機械も手に入れたようで、松居さんの怒涛の工作に期待大です!
まつ (月曜日, 17 9月 2012 22:45)
とらのすけさん
今日は、ありがとうございました!
ドーバーは、本当に”出ただけ”ですよ。バイトで貯めたお金が一気に吹き飛びましたね。別冊MCの平成2年11月号か12月号に記事として私の名前が出てますよ。何せ、誕生日がレースの当日で大学のテストをぶっちして出場したのが編集者の目に留まったようです(笑)。レースの成績ではありませんよ~。
とらのすけさんはプロの工作技師でしょうから、私にはかないません!!ボール盤とスライドバイスで疑似旋盤を楽しもうと思っておりますので、またアドバイスくださいませ~。
小林 (木曜日, 24 11月 2016 19:03)
W1SA乗りの小林と申します。オイルクーラー取り付け位置について教えてください。タイヤからの小石の跳ねなどを考えればこの位置が絶妙ですよね。ただ、オイルポンプの能力なんかが心配なのですが、大丈夫なものでしょうか?
オイルクーラーはゼファー750用、ホースは上側から入れるように取り付ける予定です。
まつ (金曜日, 25 11月 2016 07:00)
小林さん
オイルポンプ、特に問題ないと思います。他にオイルクーラー付けてる方いますけど、オイルポンプを強化してるという話も聞きませんし。そもそもそんなキットないんちゃいますかね。但しオイルポンプに損傷があれば不具合出るかもしれませんし、改造はあくまで自己責任でお願いしますね。ゼファーのコアは大きいので、サーモは必須ですよ(^^)
小林 (土曜日, 26 11月 2016 15:47)
まつさん
さっそくのお返事、ありがとうございます。僕もオイルクーラーの位置、まつさんと同じくらいの位置で取付けてみます。
ホームページ、とても参考になってます。これけらも拝見させて下さい。よろしくお願い致します